Homepage | Success Stories | Careful Pick & Place Handling
Careful Pick & Place Handling
The challenge:
Careful handling
For a packing station of brake disc and friction ring blanks in the automotive industry, it was necessary to develop a removal system that is particularly careful to the components.
The solution:
Reliable 3D recognition
An embedded vision system detects the parts that are stacked irregularly, arranged randomly and not sorted by type, and ensures that they are deposited carefully and in the correct position.
3D recognition system SKG500 – Wente/Thiedig GmbH
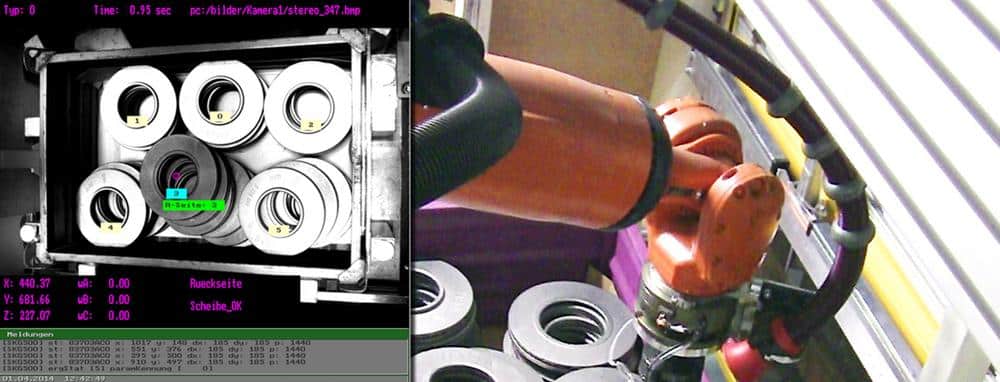
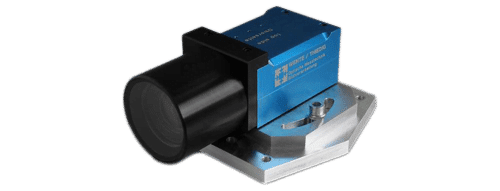
Robot-assisted parts handling for the automotive industry
Stationary system with smart camera
Together with Bertram Automation GmbH & Co. KG, Wente/Thiedig GmbH has designed a robot-guided scanning system specifically for determining the position and orientation of brake discs in heavy goods containers. For their customer in the automotive industry, the companies have now developed this system further and transferred the detection technology from the robot arm to a stationary system. In the new SKG500 scanning system, the embedded camera is installed in a fixed location and no longer in the gripper. This design significantly reduces mechanical stress.

Key Facts
Technology
3D recognition system for pick & place
Image processing in minimum space
VC Camera
VCSBC Board Camera
High processing power in an ultra-compact design: VCSBC nano-RH
The tiny camera head measures only 18 mm x 24 mm and is connected to the CPU board via an optional 30 mm or 80 mm long cable. The image is captured by a global shutter CMOS sensor and delivers razor-sharp images even in extremely fast applications. The camera has a processor clocked at 700 MHz, a 32 MB Flash EPROM and 128 MB SDRAM RAM for processing the image data. Live image output can be done via the 100 MBit Ethernet interface, which supports free programming.
About Wente/Thiedig GmbH
Wente/Thiedig GmbH, founded in Braunschweig in 1987, implements customer-specific image processing solutions for industrial applications. If required, these can be modified or supplemented by in-house developments. Machine vision systems from Wente/Thiedig GmbH are primarily used in shape and pattern recognition, for example in quality control, in the automatic control and regulation of machine processes and in the automation of measurement and control processes.
Careful Pick & Place handling
3D recognition for component-friendly pick & place solutions
Entwickeln Sie eine Vision-basierte Pick & Place-Lösung?
Talk to us about your project and the right Embedded Vision System - free of charge and without obligation.